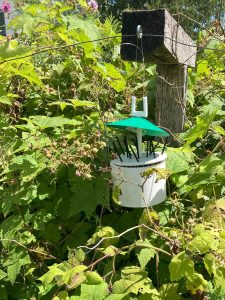
The E4 Bug Off Project: Installed in the Williams College Community Garden
Japanese beetles are an invasive species that cause considerable damage to plants across much of the United States, including in the Williams College ‘66 Envi Center
gardens. The E4 Bug Off Team—consisting of students at Harvey Mudd and Pomona colleges (Javier Perez, Linna Cubbage, Betsy Ding, Eli Schwarz, and Stephanie Huang with guidance from Profs. Steven Santana and TJ Tsai)—collaborated with the Zilkha Center on the E4 Bug Off Team Project: Mitigating Japanese Beetle Damage to develop means for repelling the beetles from campus gardens and lands before they could harm the plants. The E4 Bug Off team developed a model for a physical artifact that emits repelling scents and can be attached to trees and plants. The device, which can be created by a 3D printer, is intended to be easily built, used, durable, and human and bee friendly.
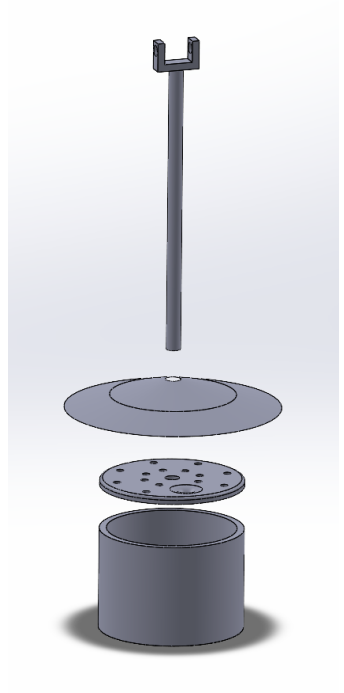
E4 Team 3D Prototype and Redesign
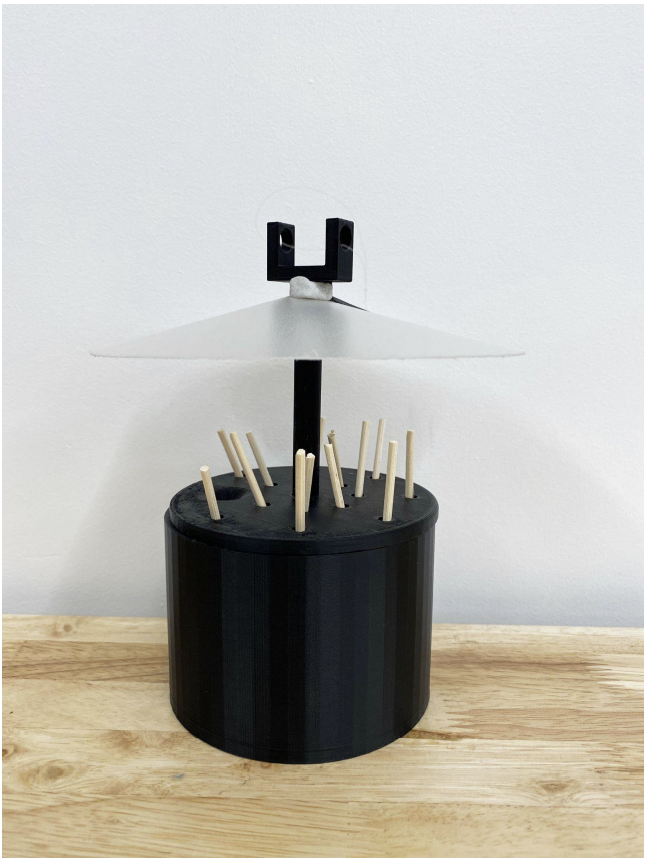
The E4 Bug Off Teams Final Prototype
The E4 Bug Off team shared the CAD files with the Zilkha Center who asked the Williams College Makerspace for assistance with printing. The first iteration of the 3D model that was created by the Makerspace consisted of a white tall body, a lid with various holes, and a short rod.
The holes in the lid are for peppermint-scented sticks and the tall body could hold additional scent liquid. Based on the research done by the E4 Bug Off team, peppermint scent was found to be a repellent of Japanese Beetles. Thus, if the scent is widely enough dispersed by the wind, it should help with keeping Japanese beetles from the area around the device. It remains to be tested, how many devices will be needed to cover the area of the gardens. It’s an innovative solution since peppermint is safer than other traps such as spectracide bags, which have low to moderate toxicity for humans. It has also been reported that such bags may also simply increase the numbers of beetles present.
The artifact also features a green cone, which protects the scent sticks from rain. It was cut out of a plastic folder by the Zilkha Center summer garden interns.
-
-
-
-
Zilkha Center: Beetle Trap
-
Zilkha Center: Beetle model 3D printed and built following the E4 Bug Off Team’s CAD files
The first prototype had a few shortcomings: its body was leaky and the rod was a little too big to fit into the lid. Zilkha Center garden interns, Martha Carlson and Evan Chester, put putty on the holes in the body to stop it from leaking and needed to heavily sand down the rod for it to fit in the base.
To create a longer-lasting solution that could also be printed in larger numbers, a new body and slightly thinner rod were designed and reprinted.
The plan is to launch the device in time for the summer 2023 Japanese Beetle season, assuming all goes well with the new sealing method. The Makerspace and Zilkha Center will share the final 3D design and list of ingredients after the final testing is complete.
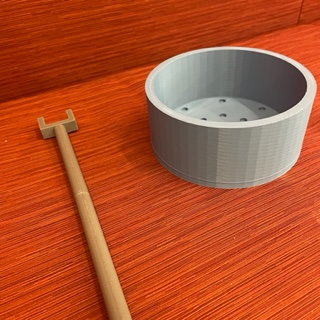
New body and thinner rod