During the sunny and pleasant reunion weekend of June 7th and 8th, the Makerspace was bustling, offering tours and hands-on making experiences to over 200 Williams alums and their families. We prepared a hands-on project that would allow people to use 3D-printed molds to cast Makerspace-themed coasters, sourced from upcycled Amazon cardboard boxes. This fun experience allowed us to share and discuss an environmentally friendly DIY project that people could easily replicate at home. People can even create their own custom molds!
During the alumni reunion weekend, the kids seemed most excited to mix the ingredients, mold the pulp, and finally clamp the coasters. They also got to take home coasters that we had prepared (and dried!) ahead of time.
Recipe
- Cardboard boxes (50g)
- Water (170g)
- PVA Glue (15g) (we used Titebond II woodworkers glue; Elmer’s white glue works, too)
Tools
- Canary corrugated cardboard cutter (an amazing kid-safe knife)
- Blender (we used an old donated blender)
- Quick release clamps
- Cheesecloth (or other thin cloth to remove liquid from pulp)
Instructions
- Cut the Amazon boxes into small pieces
- Add into the blender: 50g of cardboard, 170g of water, and 15g of glue
- Blend until it’s thick and looks like wet clay
- Assemble the 3D-printed mold: we used and modified this Pulp-it model
- Put the pulp in a cheese cloth and squeeze the excess water out
- Fill the mold with the damp pulp
- Press the pulp with your hands so that it is dense and evenly distributed in the mold
- Attach the lid to the mold
- Press the mold using a clamp
- Let it dry for 24 hours
- Carefully remove it from the mold and gently place it to dry in direct sunlight (or in front of a fan or heater vent) for about 6 hours
- It should now be 100% dry and solid
- Nice work!
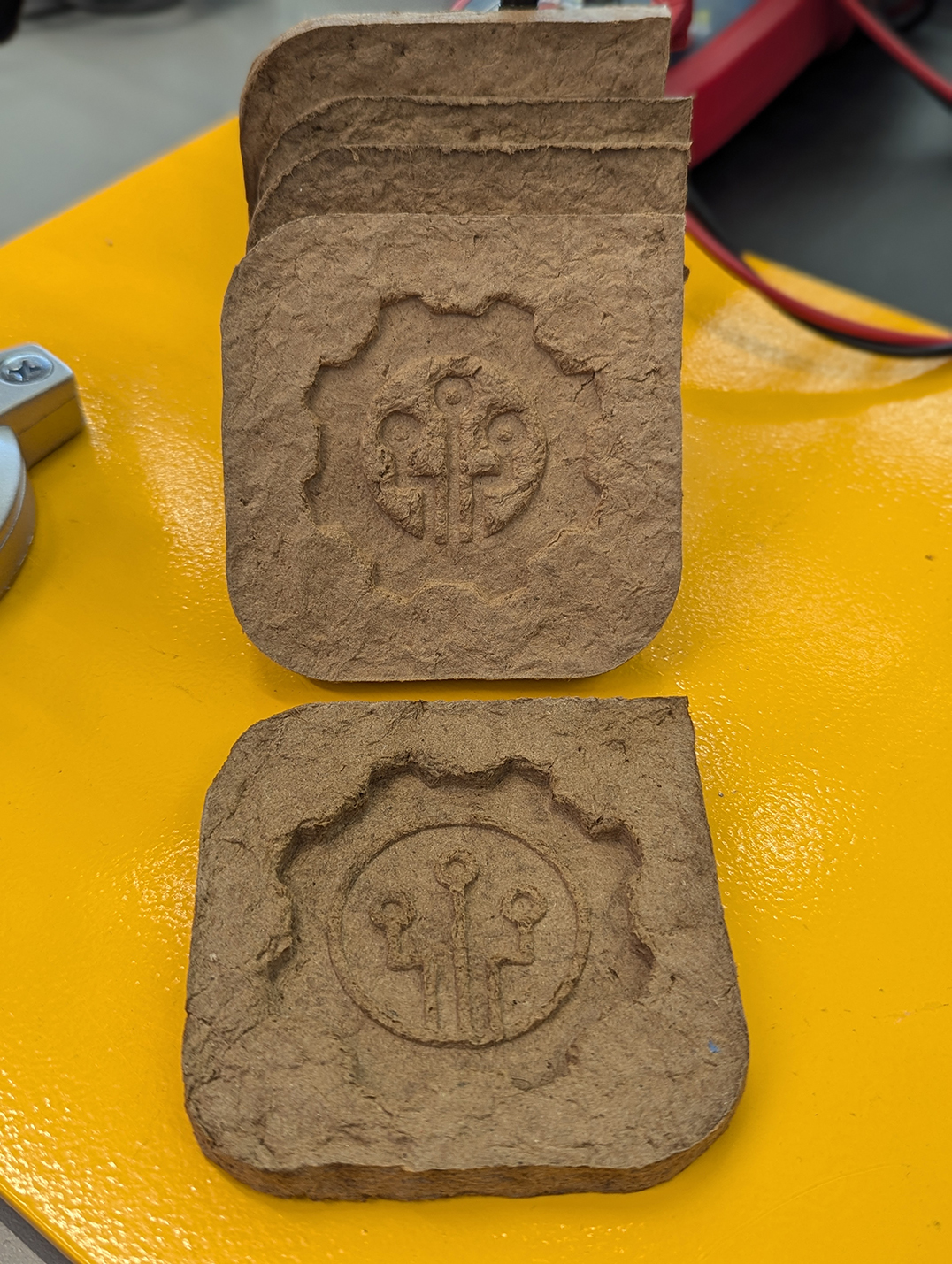
Fusion 360 software: We ended up iterating and tried inverting the extrusion of our design. Which version do you like better?
The kids had a blast making the coasters while learning about how upcycling minimizes waste in our environment. This activity demonstrated how individual action, no matter how small, may collectively impact positive change.
According to the Environmental Protection Agency…
Packaging materials account for 28.1 percent of the total municipal solid waste (MSW), amounting to 82.2 million tons of generation in 2018. This amount poses a high environmental risk and requires systemic and individual actions to mitigate the risks.
We were inspired by this Pulp-it project, and then we modified their open-source parts by using Fusion 360 software to add the Makerspace logo onto the coaster. To do this, we added an image of the logo and then extruded (raised) it about 8mm. To minimize waste, we tested our prototype models by printing it at 15% of the actual size.